Những Khái Niệm Cơ Bản Về Nguyên Lý Và Dụng Cụ Gia Công Cắt Gọt
Sự tạo hình bề mặt gia công trên máy cắt kim loại.
Các bề mặt của chi tiết gia công thường gặp trong ngành chế tạo máy rất đa dạng về kích thước và phong phú về hình dạng. Nhưng phần lớn chúng đều thuộc các dạng bề mặt cơ bản như sau: dạng các bề mặt có đường chuẩn là đường tròn, dạng các bề mặt có đường chuẩn là đường thẳng, dạng các bề mặt đặc biệt.
Dạng các bề mặt có đường chuẩn là đường tròn
Bề mặt có đường chuẩn là đường tròn là các bề mặt được tạo thành khi cho đường sinh chuyển động tương đối xung quanh đường chuẩn tròn (hình 1.3) với đặc trưng cơ bản là có trục đối xứng, hoặc tâm đối xứng.
- Bề mặt trụ là bề mặt tròn xoay có đường sinh thẳng song song với đường tâm khối trụ và đường chuẩn là đường tròn (hình 1.1 a).
- Bề mặt côn cũng là bề mặt tròn xoay có đường sinh thẳng giao với đường tâm khối côn và đường chuẩn là các đường tròn (hình 1.1 b).
- Nếu đường sinh là đường cong (hình 1.2 a) sẽ tạo thành bề mặt tròn xoay có hình tang trống. Bề mặt hình dạng ren là bề mặt đặc thù của ngành chế tạo máy có đường sinh là đường gẫy khúc, đường chuẩn là đường tròn và đường thẳng song song với đường tâm khối ren (hình 1.2 b).
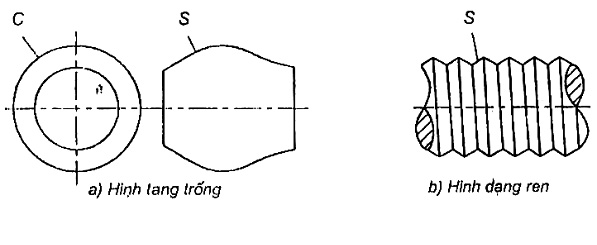
Dạng bề mặt có đường chuẩn là đường thẳng
Các bề mặt có đường chuẩn là đường thẳng gồm những bề mặt được qui ước tạo thành bởi đường sinh là đường thẳng, đường cong hoặc đường gấp khúc chuyển động trượt trên đường chuẩn là đường thẳng được trình bày trên hình 1.3 (a).
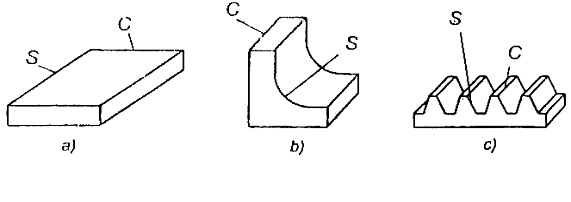
Dạng bề mặt đặc biệt (cam, cánh tuoocbin, răng thân khai ..)
Các dạng bề mặt đặc biệt là các bề mặt không gian phức tạp có đường chuẩn là đường cong hoặc đường thẳng, đường sinh là các đường thẳng hoặc đường thân khai.. Tuy nhiên việc phân biệt đường sinh và đường chuẩn chỉ có tính chất tương đối. Tùy thuộc vào độ phức tạp của bề mặt gia công, lựa chọn đường sinh và đường chuẩn sẽ đưa đến sơ đồ động của máy có độ phức tạp khác nhau. Các bề mặt đặc biệt này được trình bày trên hình 1.4.
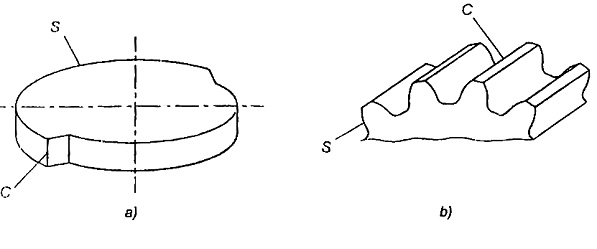
Để hình thành các dạng bề mặt khác nhau của chi tiết gia công, trong ngành chế tạo máy cần thiết phải tạo ra các đường sinh và đường chuẩn tương ứng.
Nếu các bề mặt gia công được tạo thành từ đường sinh là đường thẳng, đường tròn, đường xoắn acsimet hoặc đường thân khai… thì máy cắt kim loại chỉ cần phối hợp hai chuyển động đơn giản đó là: thẳng và quay tròn đều.
Để tạo thành đường sinh là đường hypecbon, đường elip, đường xoắn log,.. máy cắt kim loại cần phải phối hợp hai chuyển động phức tạp đó là: thẳng và quay tròn không.
Các mặt trên vật gia công
Bất kỳ phương pháp gia công nào, quá trình hớt bỏ dần lớp lượng dư gia công cơ (quá trình cắt) đều hình thành trên chi tiết 3 bề mặt có đặc điểm khác nhau. Xét tại một thời điểm nào đó trong quá trình gia công (khi tiện), ba bề mặt trên được phân biệt như sau:
- Mặt sẽ gia công: là bề mặt của phôi mà dao sẽ cắt đến theo qui luật chuyển động. Tính chất của bề mặt này là tính chất bề mặt phôi.
- Mặt đã gia công: là bề mặt trên chi tiết mà dao đã cắt qua. Tính chất của bề mặt này là phản ánh những kết quả của các hiện tượng cơ lý trong quá trình cắt.
- Mặt đang gia công: là bề mặt trên chi tiết mà lưỡi dao đang trực tiếp thực hiện tách phoi. Cũng là mặt nối tiếp giữa mặt đã gia công và mặt sẽ gia công. Trên bề mặt này đang diễn ra các hiện tượng phức tạp.
- Vùng cắt : Là phần kim loại cuả chi tiết vừa được tách ra ở gần mũi dao và lưỡi cắt nhưng chưa thoát ra ngoài. Đây là vùng đang xảy ra các quá trình cơ lý phức tạp.

Những yêu cầu cơ bản đối với vật liệu làm phần cắt của dao.
a. Độ cứng:
b. Độ bền cơ học:
c. Tính chịu nóng:
d. Tính chịu mài mòn:
e. Tính công nghệ:
Một cách lí tưởng, vật liệu dụng cụ cắt cần phải đảm bảo các yêu cầu sau đây:
- Độ cứng đâm xuyên cao ở nhiệt độ cao để tăng tính chống mòn do cào sước;
- Độ bền biến dạng cao để bảo toàn hình dáng lưỡi cắt khỏi sự biến dạng hoặc cong oằn dưới tác động của ứng suất phát sinh khi tạo phôi;
- Tính dẻo dai và chịu va đập để chống lại sự mẻ vỡ lưỡi cắt, đặc biệt khi cắt không liên tục (có va đập);
- Tính trơ hóa học (ái lực hóa học thấp) với vật liệu gia công để chống lại mòn oxy hóa, mòn hóa học và mòn khuyếch tán;
- Tính dẫn nhiệt cao để giảm nhiệt cắt gần lưỡi cắt;
- Độ bền mỏi cao, đặc biệt với các dụng cụ được sử dụng cắt không liên tục;
- Độ bền mỏi nhiệt cao (thermal shock resistance) để bảo vệ dụng cụ không bị vỡ khi cắt không liên tục;
- Độ bền hình dạng cao (high stiffness) để đảm bảo độ chính xác gia công; và
- Tính trơn trượt thỏa đáng (adequate lubricity) – ma sát nhỏ với vật liệu gia công để hạn chế việc hình thành lẹo dao, đặc biệt khi gia công vật liệu mềm dẻo.